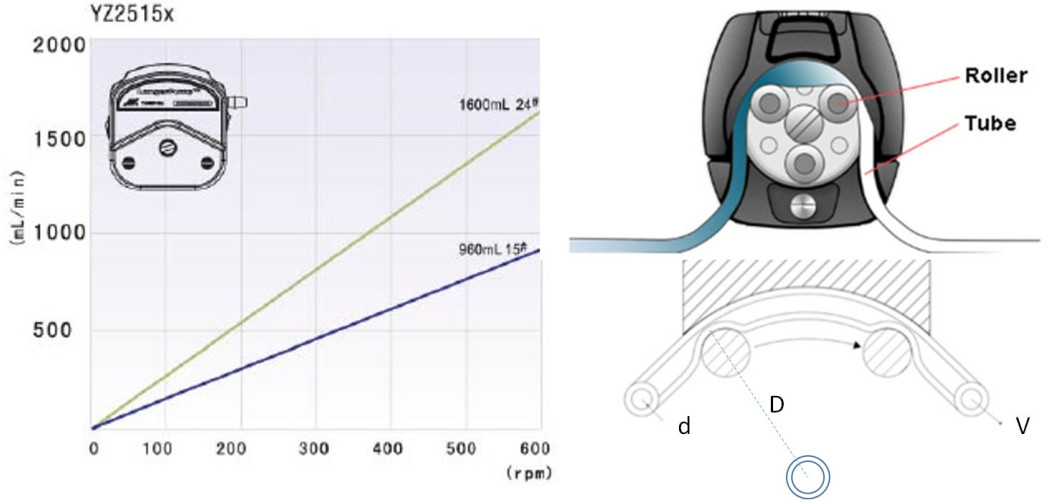
The flow rate of a specific peristatic pump is determined by three major parameters: the rotation speed (N rpm) of the rotor shaft, the inner diameter (d cm) of the hose, and the diameter (D cm) of the roller assembly. The flow rate V (mL/min) can be expressed in the following formula.
V = [p (d/2)2] [p(D+2T-d)b]N
Where T is the wall thickness of hose in cm (centimeter), which is usually much smaller than D, and b is the effective fraction for a cycle of rotor rotation. The flow rate formula above indicates the following general conclusions under normal run conditions:
- The volume flow rate is proportional to the rotor speed N.
- The volume
flow rate is proportional to the square of the hose diameter.
- The volume
flow rate is closely proportional to the diameter of the roller track arc.
However, other factors need to be considered, since the
effective fraction b is
dependent on the number of rollers and roller diameters, the back pressure of
the inlet side (hose diameter and length, viscosity of fluid, and hose
material, etc.), and the rotation speed N when N is too big.
As a numerical example, we can consider a system when being operated at N = 10 rpm; suppose the tubing inner diameter is d = 0.48 cm, wall thickness 0.16 cm, and the diameter of the roller assembly D = 4.0 cm, and b = 0.8 (typically b in the range of 0.6-0.8). So the flow rate is:
V = 3.14 x (0.48/2)2 x 3.14 x (4.0 +2x0.16- 0.48) x 0.8 x 10
= 17.46 mL/min
In application practice, the flow rate for a specific pump system should be calibrated, so a calibration curve can be plotted as shown in the following example. A simplified flow rate formula can be obtained:
V = kN
where
17 Comment(s)
Các cược thể thao trên FB88 rất đa dạng, tôi có thể chọn cược từ nhiều môn thể thao khác nhau.
Tôi luôn cảm thấy an tâm khi chơi tại FB88, họ rất chú trọng bảo mật thông tin người chơi.
FB88 luôn cung cấp các sản phẩm game chất lượng cao và dịch vụ khách hàng tốt.
1
1
1
1
1
Hệ thống bảo mật của họ rất chặt chẽ, giúp tôi cảm thấy yên tâm khi chơi.
Tôi cảm thấy rất thoải mái khi chơi tại FB88, họ luôn đem lại một trải nghiệm tuyệt vời.
Khuyến mãi của FB88 rất phong phú, tôi luôn có cơ hội nhận thêm phần thưởng.
1
1
1
1
1
Trải nghiệm chơi game trên FB88 luôn là những khoảnh khắc thú vị và đáng nhớ.
FB88 cung cấp rất nhiều loại game casino, không thiếu lựa chọn nào.
Trò chơi trên FB88 rất dễ chơi, quy tắc rõ ràng và dễ hiểu.
1
1
1
1
1
Trường Tiểu học Nguyễn Trung Trực được thành lập năm 1985 có địa chỉ tại 9A Phạm Hồng Thái, phường Nguyễn Trung Trực, quận Ba Đình, Hà Nội (Nay thành phường Trúc Bạch). Trường hoạt động dưới sự quản lý của UBND quận Ba Đình và Phòng Giáo dục và Đào tạo Ba Đình. Trường được xây dựng khang trang trên diện tích hơn 3000 m2 với đủ các phòng học và phòng chức năng cho các hoạt động học tập, vui chơi, giải trí của học sinh.
Địa chỉ: Số 9A Phạm Hồng Thái - Ba Đình - Hà Nội
Email: c1nguyentrungtruc-bd@hanoiedu.vn
website: https://c1nguyentrungtruc.badinh.edu.vn/
Điện thoại: 438261441
1
1
1
1
1
Trường Tiểu học Nguyễn Trung Trực được thành lập năm 1985 có địa chỉ tại 9A Phạm Hồng Thái, phường Nguyễn Trung Trực, quận Ba Đình, Hà Nội (Nay thành phường Trúc Bạch). Trường hoạt động dưới sự quản lý của UBND quận Ba Đình và Phòng Giáo dục và Đào tạo Ba Đình. Trường được xây dựng khang trang trên diện tích hơn 3000 m2 với đủ các phòng học và phòng chức năng cho các hoạt động học tập, vui chơi, giải trí của học sinh.
Địa chỉ: Số 9A Phạm Hồng Thái - Ba Đình - Hà Nội
Email: kumu.io@kumu.io
website: Https://kumu.io/NhacaiFB88betB88S/nhacaifb88betb88s#nhacaifb88betb88s
Điện thoại: 438261441
1
1
1
1
1
Trường Tiểu học Nguyễn Trung Trực được thành lập năm 1985 có địa chỉ tại 9A Phạm Hồng Thái, phường Nguyễn Trung Trực, quận Ba Đình, Hà Nội (Nay thành phường Trúc Bạch). Trường hoạt động dưới sự quản lý của UBND quận Ba Đình và Phòng Giáo dục và Đào tạo Ba Đình. Trường được xây dựng khang trang trên diện tích hơn 3000 m2 với đủ các phòng học và phòng chức năng cho các hoạt động học tập, vui chơi, giải trí của học sinh.
Địa chỉ: Số 9A Phạm Hồng Thái - Ba Đình - Hà Nội
Email: kumu.io@kumu.io
website: Https://kumu.io/NhacaiFB88betB88S/nhacaifb88betb88s#nhacaifb88betb88s
Điện thoại: 438261441
1
1
1
Trường Tiểu học Nguyễn Trung Trực được thành lập năm 1985 có địa chỉ tại 9A Phạm Hồng Thái, phường Nguyễn Trung Trực, quận Ba Đình, Hà Nội (Nay thành phường Trúc Bạch). Trường hoạt động dưới sự quản lý của UBND quận Ba Đình và Phòng Giáo dục và Đào tạo Ba Đình. Trường được xây dựng khang trang trên diện tích hơn 3000 m2 với đủ các phòng học và phòng chức năng cho các hoạt động học tập, vui chơi, giải trí của học sinh.
Địa chỉ: Số 9A Phạm Hồng Thái - Ba Đình - Hà Nội
Email: s666@s666s666s.com
website: Https://s666s666s.com/
Điện thoại: 438261441
1
1
1
Trường Tiểu học Nguyễn Trung Trực được thành lập năm 1985 có địa chỉ tại 9A Phạm Hồng Thái, phường Nguyễn Trung Trực, quận Ba Đình, Hà Nội (Nay thành phường Trúc Bạch). Trường hoạt động dưới sự quản lý của UBND quận Ba Đình và Phòng Giáo dục và Đào tạo Ba Đình. Trường được xây dựng khang trang trên diện tích hơn 3000 m2 với đủ các phòng học và phòng chức năng cho các hoạt động học tập, vui chơi, giải trí của học sinh.
Địa chỉ: Số 9A Phạm Hồng Thái - Ba Đình - Hà Nội
Email: s666@s666s666s.com
website: Https://s666s666s.com/
Điện thoại: 438261441
1
1
Trường Tiểu học Nguyễn Trung Trực được thành lập năm 1985 có địa chỉ tại 9A Phạm Hồng Thái, phường Nguyễn Trung Trực, quận Ba Đình, Hà Nội (Nay thành phường Trúc Bạch). Trường hoạt động dưới sự quản lý của UBND quận Ba Đình và Phòng Giáo dục và Đào tạo Ba Đình. Trường được xây dựng khang trang trên diện tích hơn 3000 m2 với đủ các phòng học và phòng chức năng cho các hoạt động học tập, vui chơi, giải trí của học sinh.
Địa chỉ: Số 9A Phạm Hồng Thái - Ba Đình - Hà Nội
Email: s666@s666s666s.com
website: Https://s666s666s.com/
Điện thoại: 438261441
1
Trường Tiểu học Nguyễn Trung Trực được thành lập năm 1985 có địa chỉ tại 9A Phạm Hồng Thái, phường Nguyễn Trung Trực, quận Ba Đình, Hà Nội (Nay thành phường Trúc Bạch). Trường hoạt động dưới sự quản lý của UBND quận Ba Đình và Phòng Giáo dục và Đào tạo Ba Đình. Trường được xây dựng khang trang trên diện tích hơn 3000 m2 với đủ các phòng học và phòng chức năng cho các hoạt động học tập, vui chơi, giải trí của học sinh.
Địa chỉ: Số 9A Phạm Hồng Thái - Ba Đình - Hà Nội
Email: s666@s666s666s.com
website: Https://s666s666s.com/
Điện thoại: 438261441
1
Trường Tiểu học Nguyễn Trung Trực được thành lập năm 1985 có địa chỉ tại 9A Phạm Hồng Thái, phường Nguyễn Trung Trực, quận Ba Đình, Hà Nội (Nay thành phường Trúc Bạch). Trường hoạt động dưới sự quản lý của UBND quận Ba Đình và Phòng Giáo dục và Đào tạo Ba Đình. Trường được xây dựng khang trang trên diện tích hơn 3000 m2 với đủ các phòng học và phòng chức năng cho các hoạt động học tập, vui chơi, giải trí của học sinh.
Địa chỉ: Số 9A Phạm Hồng Thái - Ba Đình - Hà Nội
Email: s666@s666s666s.com
website: Https://s666s666s.com/
Điện thoại: 438261441
1
Insightful and so easy to understand. I didn’t expect it to be this helpful.
1
1
1
1
1
1
1
1
1
1
1
Leave a Comment